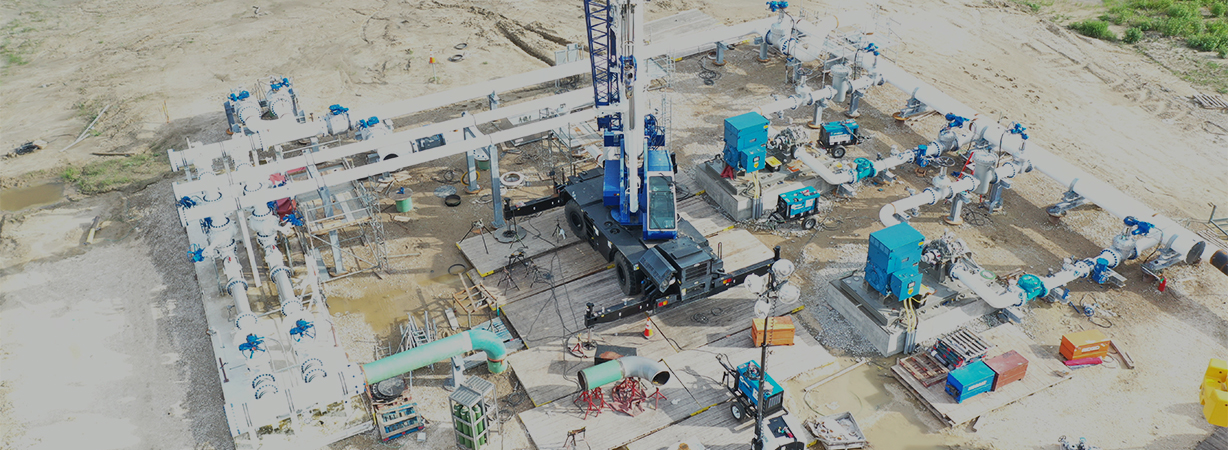
Project Overview
P&E Company recently completed an $18 million mechanical project on a crude rail unloading/blending terminal in Port Arthur, Texas, that included process piping, utility piping, equipment setting, structural steel and instrumentation—key capabilities in P&E Company’s toolbox.
The scope of the project including the mechanical work was for a $130 million, 320-acre greenfield project by the USD Group, a mid-stream energy infrastructure company, and was managed by P&E Company’s sister organization, P&E Solutions. (Read more about P&E Solution’s EPC project management on the project here.)
Meeting any Code
For the new Port Arthur terminal, P&E Company installed nearly 30, 000 feet of pipe, ranging in size from 1/2 inch to 42 inches. The project featured 13,340 welds, which were completed with a weld-rejection rate of 0.02%, which is much lower than the industry standard of 3%. Piping on the project was installed to codes ASME B31.1 (power piping), B31.3 (process piping), B31.4 (pipeline transportation systems for liquids and slurries) and API-1104 (American Petroleum Institute’s global standard for welding of pipelines and related facilities).
P&E Company’s work went far beyond piping: The team, led by project manager Timothy E. Farnham, also set and assembled pumps, meter skids, air compressor skids, sample skids, cooling towers, condensate skids, quality control (QC) skids, vessels, exchangers, and motor control center (MCC) buildings. P&E installed more than 500 pipe supports and a pipe bridge as well as miscellaneous platforms, stairs and ladders. The Port Arthur P&E Company crew also installed control valves, motor operated valves, pressure relief valves, pressure transmitters, ultrasonic flow transmitters, level transmitters, level gauges and pressure gauges.
P&E’s mechanical work home-court advantage
P&E Company kept this complex and multi-faceted project on-schedule by moving almost 20 percent of the work to its own shop in Wichita, Kansas. When weather conditions in Port Arthur threatened progress, P&E Company was able to continue moving ahead inside its shop at P&E’s headquarters. P&E Company’s Kansas-based shop fabrication included modular pipe systems, air compressor skids, QC skids and miscellaneous structural steel.
Safe to the last hour
With a culture that emphasizes zero at-risk behaviors, a drug-screened work force and NCCCO-certified equipment operators, P&E Company was able to complete the project with more than 130,000 work hours and zero OSHA-recordable incidents.
The team for this project included Superintendent Don Henry, Jr.; Assistant Superintendents Kevin Logan and Bob Cargile; Field Quality Control Manager Eric Cales; and Office Manager Becky Henry.
If you’ve got a similar job you need done on-time, on-budget and without incident, reach out.